Noise and coping strategies in hydraulic transmission systems
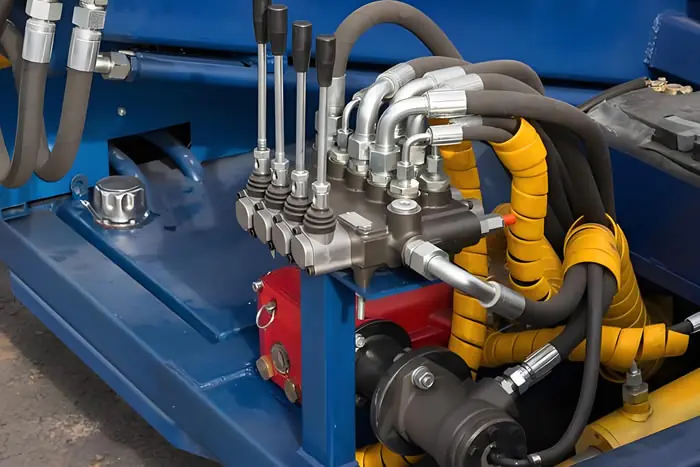
The noise of the hydraulic transmission system is generated by the motor, hydraulic pump, valve auxiliary devices and hydraulic piping composed of closed circuit.
Because in this closed circuit system, the working state of the hydraulic oil due to the flow and pressure pulsation impact cavities turbulence and eddy current and produce fluid noise, and at the same time transmitted to the support base parts and cause vibration, the formation of mechanical noise.
Noise source of hydraulic transmission system and its influencing factors
In general, the noise of the hydraulic transmission system, there are fluid power noise, mechanical vibration noise, pipe resonance noise and resonance noise due to vibration and noise caused by the support parts of the tank and other resonance noise.
The motor of the motor is the power source, motor noise is the main factor of mechanical noise.
Motor noise of oil pump
The noise sources are mainly aerodynamic noise generated by the cooling fan, rotor unbalanced operation, electromagnetic vibration, commutator, rectifier, and various parts (such as casing, end caps) and other vibration-induced noise.
Noise of hydraulic pump and Hydraulic Motor:
Mechanical noise. Due to the hydraulic pump and hydraulic motor work process, each working chamber of oil pressure cyclic fluctuations and pressure oil pressure area of the working chamber of the sharp cyclic changes in the parts shell catty road to produce a proposed dynamic and noise mountain in the oil supply is not enough to produce cavitation, cavitation phenomenon, caused by intense vibration, this excitation force is irregular gear pumps, gear mesh noise with the load speed tooth roughness increases and enhances the processing of gears. Viscosity has a great relationship.
Fluid noise. hydraulic pumps and hydraulic motors in the working process, will produce different degrees of energy pulsation, this pulsation is transformed into pressure pulsation when encountered obstruction, thus generating forced vibration of the container. The formation of the liquid noise this noise spectrum is broader, its pulsation frequency and the number of pulsations per unit of time flow is directly proportional to the number of pulsations. In addition, hydraulic pumps and hydraulic motors of high-frequency noise is caused by the formation of eddy currents, cavities or impact in the work process, it is not regular, less intense.
hydraulic Valve noise:
Various valve body of the hydraulic valve is a moving body, and many of the valve spool in the work are relying on the action of the spring, so it is easy to produce vibration, which occurs mechanical noise. These according to the different functions in its system, the mechanical vibration generated is not the same, directional valve commutation issued by the impact of the sound is instantaneous; relief valve relief valve spool generated by high-frequency vibration is continuous, if the outside world to interfere with the rate of just for the state of the formation of the damping frequency, it will cause resonance, increasing the noise. Resonance caused by high-frequency noise, the frequency range of 1-8kHz, sound pressure level of 90dB or more, with a clear peak.
Piping noise
In the hydraulic transmission piping system, the unstable flow of the fluid is often occurring, this unstable flow is due to the composition of certain components of the system or caused by external interference, etc. In general, for a reasonable hydraulic system, this unstable state is only temporary, it will eventually transition to a new stable state of the short period of time, the pipeline will produce internal shock waves. Under certain conditions, the combination of piping and pumps or valves will produce a continuous vibration of the oil in the piping system, when the length of the pipeline is just equal to the resonance of the pipeline isometric, it will produce a strong high-frequency noise.
Fuel tank noise
The oil tank is a device with a large area of injection, which is the main component for transmitting and expanding noise. Its noise is often due to other devices to stimulate and produce, and the noise is large, if the hydraulic pump motor is directly mounted on the top cover of the tank, the pump or motor vibration will cause oil vibration.
Hydraulic drive system noise control and measures
To reasonably select the motor and hydraulic pump. Motor, hydraulic pump is the main noise source of the hydraulic transmission system. In the hydraulic drive system design should have an understanding of its performance and noise characteristics, and take relative measures.
Reduce motor noise
Must be in accordance with China's motor noise limit standard selection of the corresponding fan shape. Reduce the fan can achieve better noise reduction. Generally speaking, the fan diameter changes with the noise changes have a relationship, in order to reduce the suction resistance, should often clean and check the oil filter, to prevent the phenomenon of blocking the thick, depending on the region and seasonal differences, respectively, choose different grades of oil, or the use of fixed preheating device. For the configuration of the oil pipe should also pay attention to the hydraulic system pipeline configuration square suction port of the duplex pump should be referenced to the preparation, otherwise, the oil is easy to flow to the large-capacity pump low-pressure pumps, and small-capacity pumps are prone to cavitation.
In addition, the tank oil is not enough, the oil filter exposed oil surface, hydraulic pumps will also be vortex-like and sucked into a large amount of air so the opening of the oil pipe should be inserted into the oil. Comparison of the noise factor, generally by changing the fan diameter. For example, a reduction in the outer diameter of the fan reduces the noise. In addition, the use of single backward tilting wing type plastic or alloy fan with high internal damping is also more effective. Can also change the number of blades to solve the noise generated by the resonance of the blades and the number of duct grooves. Secondly, we should pay attention to reduce electromagnetic noise, the main measures are to choose high-precision motor to stabilize the power supply voltage, and timely fastening of easy to loose parts such as the wind cover screws, etc., to prevent resonance. Muffling and sound insulation measures can be used again, without affecting the motor ventilation and heat dissipation under the premise of taking the muffling sound insulation cover or resistance muffler to reduce noise.
Choose the pump with less pulsation
Oil pump discharge oil with pulsation, this pulsating liquid flow will stimulate mechanical vibration and cause noise, so try to choose a small pulsation of the pump. For example, the same gear pump, internal gear pump than external gear pump pulsation is much smaller.
Try to prevent cavitation in the system
Hydraulic drive system to produce cavitation, mainly due to air dissolved in the oil or the formation of small bubbles mixed in the oil. When the local pressure is reduced to the air separation pressure of the oil, then the air dissolved in the working oil will be separated in large quantities, forming cavities. If this bubble enters the high-pressure area, it will rupture, generating a high-frequency shock pressure with a large amplitude in the local range, causing high-frequency noise. This cavitation phenomenon is caused by the pump suction resistance is too large, therefore, to choose a good suction performance of the hydraulic pump, while as far as possible to make the suction pipe short thick straight.
Reduce or avoid the suction pipe mutation
Reasonable design of the tank structure is an effective way to remove air bubbles in the oil. Usually the oil back to the tank with air bubbles, as long as there is enough product to be greater than or equal to the maximum flow rate of two minutes in the system, consciously increase the residence time of the oil, so that the air bubbles in the oil is fully released.
Prevent vibration of piping system
The vibration of the piping system to its vibration nature and amplitude and pipe length, pipe diameter material, pipe support form, position of the linkage. In order to prevent resonance, to avoid the inherent frequency of the piping system, usually controlled in the excitation frequency outside a certain range. In most cases, the excitation frequency can not be arbitrarily changed, so the inherent frequency of the piping system should be adjusted. For example, in the appropriate location to add support to change the valve body installation position and so on. Approximate calculation of the inherent frequency of the piping system can be referred to the relevant manuals, but according to the actual situation of the piping support as far as possible in the design of a solid platform. In order to prevent the vibration of the piping system, you can also take the buffer sound insulation vibration isolation measures, such as part of the use of rubber hoses to drain the pipe and its support parts and neighboring components separated, the use of acoustic materials to cover the pipeline to increase the rigidity of the pipeline and so on.
Reduce the fluid noise of the valve in the system
When the reversing valve is reversed, the fluid is rapidly closed and opened. Due to inertia, it will cause hydraulic shock, the value of which depends on the rate of change of pressure. Therefore, reduce the speed of movement, appropriate extension of the commutation time, you can reduce the vibration, installation of reversing valves with taper, additional buffer devices and the use of electro-hydraulic reversing valves can moderate the impact.
The flow rate noise of the relief valve and the main spool of the valve body, the main valve seat and other parts of the geometry. Flow through the throttle hole of the jet stream, the first impact compensation and loss of part of the kinetic energy, so increase the diameter to help block the ability of the jet stream. The difference is also related to the flow noise. Difference increases, the liquid jet angle also increases. So from the ring throttle orifice and the center of the liquid jet, in the horizontal direction of the liquid flow velocity before rushing to the pressure compensation can offset each other partially. Loss of part of the kinetic energy, you can reduce the flow rate of noise, but due to the throttle orifice angle is too sharp, will make the noise increase, for this reason, can be used in a kind of main spool for the cone valve structure of the low-noise relief valve. Due to the smaller, can better prevent the throttle port part of the turbulent flow so that the noise is reduced.
Flow valve due to the liquid flow force and flow rate changes, so that the throttle valve issued when the noise is large and small. If the throttle valve before and after the pressure and flow rate changes are large, in addition to the increase in the flow rate noise, but also will produce a large eddy current noise, can be graded throttling or select the appropriate flow check valve vibration and impact, the size of the spring and spring-related, spring is too hard, the adjustable force is still large, vibration and impact sound is also large. For this reason, the appropriate spring stiffness should be selected to reduce the flow rate through the check valve, thereby reducing the noise.
Reduce the noise of structural vibration:
Design of oil-hydraulic transmission structure, in order to compact structure, reduce the occupied area, often the pump motor installed in the tank. In this way, the vibration of the pump and motor can easily excite the tank to produce a lot of noise. In order to reduce vibration, it is best to place the motor and the pump alone or in the installation of some sound insulation and vibration damping measures, such as placing a rubber mat between the motor pump and the cover for vibration isolation, and the pump coupled with the oil pipe into a rubber pipe or a pipe covered with sound insulation materials, and placed at the appropriate distance on the elastic support fixed pipeline to improve the rigidity of the oil tank.
Conclusion
The working condition of the hydraulic transmission system is relatively complex, due to a variety of hydraulic transmission system in the performance specifications transmission mode and structural features, etc. are very different, the degree of noise generated will also be very different. Therefore, from the theoretical analysis of hydraulic transmission noise causes and control methods, it is often difficult to receive the expected results, must be specific for the specific structure of the hydraulic transmission, especially the specific production and use of the situation, targeted and comprehensive use of a variety of measures to reduce the noise, in order to effectively control the noise of the hydraulic transmission system.
Why Choose XingYing Hydraulic as Your Supplier?
1.Direct from Manufacturer: Benefit from competitive pricing on top-quality hydraulic products, sourced directly from our factory in China.
2.Custom Solutions: Our expertise allows us to tailor hydraulic components to your precise requirements, ensuring optimal performance.
3.Reliable Supply: Count on us as your trusted supplier for consistent quality and timely delivery, backed by our reputation in the industry.