Hydraulic Vane Pumps: Understanding and Preventing Cavitation Damage
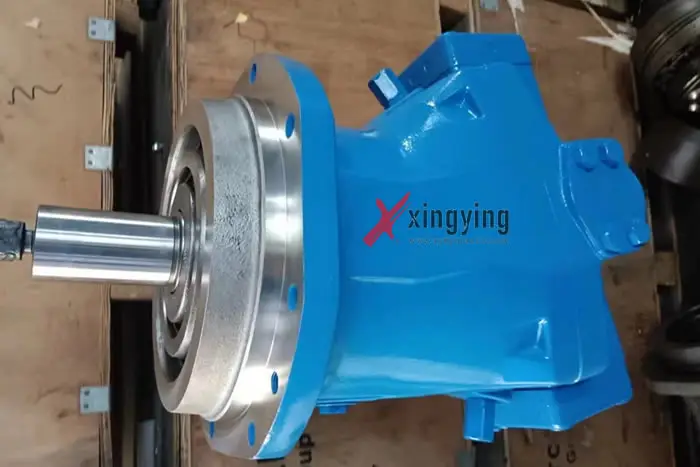
Cavitation in hydraulic Vane Pumps
Cavitation is a phenomenon that occurs in hydraulic pumps when the pressure of a liquid is lower than its vapor pressure, causing the liquid to vaporize
and the formation of air bubbles.
When these bubbles reach areas of High Pressure, they rupture, implode and create a shock wave that can damage the pump.
The root cause of the problem is a restriction in the pump suction line. This restriction increases the vacuum level that
causing air trapped in the fluid to be pumped out and form bubbles in the suction line.
As these bubbles pass from the low-pressure side of the pump to the high-pressure side, they burst under pressure and implode.
This causes small explosions and high heat, which damages the metal port plates and sometimes melts the metal, compromising its integrity.
As a result of this continuous state, the pump produces a high-pitched whining noise.
Over time, the metal is gradually removed with the hydraulic fluid, leaving an empty depression in the port plate.
Repeated occurrences of this phenomenon can lead to hole enlargement and eventual pump failure.
Aeration of the fluid can also cause cavitation, but it is accompanied by other symptoms such as a more erratic noise,
like grinding or rumbling. Aeration can be caused by air entering due to a leak in the suction line, or by air entering from the outside, such as through an unsubmerged reservoir.
for example through a return line that is not submerged below the soil surface of the reservoir.
In the case of aeration, foam can be seen visually in the oil and reservoir.
Symptoms of cavitation in hydraulic Vane pumps
Noise: Cavitation can cause the pump to make a loud rattling noise.
Vibration: The pump may vibrate excessively due to shock waves created by the bursting of air bubbles.
Reduced performance: Cavitation reduces the flow and pressure of the pump.
Damage to the pump: Imploding air bubbles can damage the pump's impeller, casing and other components.
Types of Cavitation
There are two main types of cavitation:
Vapor Cavitation: This is the most common type of cavitation and occurs when the pressure of a liquid is lower than its vapor pressure,
causing bubbles to form in the liquid. These bubbles then burst violently, damaging the surrounding material.
Cavitation is common in propellers, pumps and valves.
Gaseous Cavitation: This type of cavitation occurs when a dissolved gas escapes from solution due to a drop in pressure.
Gaseous cavitation is less common than vapor cavitation, but can still cause damage to materials.
Cavitation is common in pipes and fluid bearings.
In addition to these two main types, there are several other types of cavitation, such as:
Inertial cavitation: This type occurs when a fluid accelerates or decelerates rapidly, which can cause bubbles to form in the fluid.
Acoustic cavitation: this type of cavitation occurs when sound waves create bubbles in a liquid.
Frictional Cavitation: This type of cavitation occurs when two surfaces rub against each other in a liquid, which causes bubbles to form in the liquid.
How to prevent cavitation in Hydraulic Vane Pumps
Material Reinforcement:
(1) Optimize the material of the vane pump flow distribution disk, choose a higher strength
material than aluminum alloy to enhance the anti-cavitation ability under high pressure and high speed conditions.
Distributor disk surface plating can also improve its strength, but need to carefully consider the manufacturing cost and product quality.
Damping holes or grooves:
(2) Small damping holes or grooves are introduced at potentially cavitation-prone locations to slow the precipitation of air bubbles during blast impact.
This method can help minimize structural damage to the pump body caused by bubble rupture.
However, changes in the manufacturing process and increased processing costs need to be carefully considered.
Fluid dynamics optimization:
(3) Solve the cavitation problem caused by unstable oil flow in the pump chamber by optimizing the stator curve.
Improvement of manufacturing accuracy and post-processing methods.
This approach aims to enhance the overall dynamic characteristics of the vane pump, to
minimize the instability of fluid movement in the pump chamber and reduce the damage to the flow disk caused by cavitation.
In essence, proactively preventing cavitation through thorough maintenance practices is not just a
advice - it's a strategic investment in the continued efficiency and longevity of your pump.
Rely on us for unrivaled advice and access to the latest remote condition monitoring technoLogy to
ensure your pumps run at peak performance for years to come. If you need help, please contact us.
Why Choose XingYing Hydraulic as Your Supplier?
1.Direct from Manufacturer: Benefit from competitive pricing on top-quality hydraulic products, sourced directly from our factory in China.
2.Custom Solutions: Our expertise allows us to tailor hydraulic components to your precise requirements, ensuring optimal performance.
3.Reliable Supply: Count on us as your trusted supplier for consistent quality and timely delivery, backed by our reputation in the industry.