How to reduce the loss of pressure energy in hydraulic motors
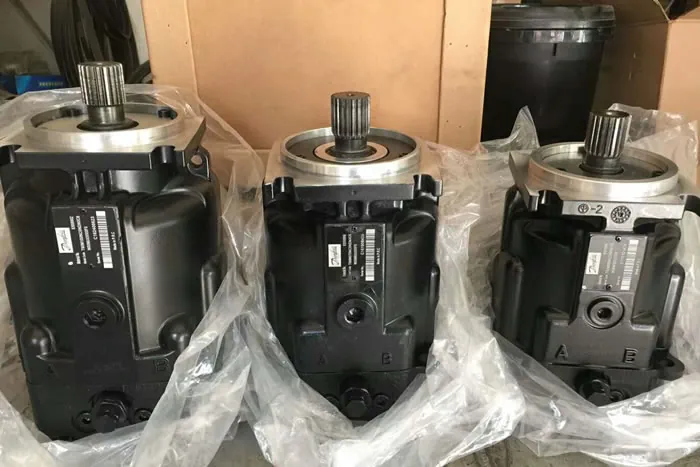
Reducing Pressure Energy Loss in hydraulic motors: Insights and Strategies
Hydraulic Motors play a pivotal role in various industrial applications by converting hydraulic energy into mechanical energy. Despite their utility, one of the significant challenges they face is the excessive loss of pressure energy, which hampers their efficiency. If these losses can be minimized, the energy conversion efficiency of hydraulic motors can be significantly improved. This article delves into various strategies to reduce pressure energy loss in hydraulic motors, focusing on internal structural improvements, material advancements, and maintenance practices.
Internal Structural Improvements
The primary step in reducing pressure energy loss is to optimize the internal structure of the hydraulic motor. By focusing on the design and configuration of internal components, the system can achieve better efficiency. One effective approach is the utilization of integrated circuit channels. Integrated circuit channels help streamline the flow of hydraulic fluid, reducing turbulence and resistance within the system. This streamlined flow minimizes energy loss due to pressure drops across various components.
Additionally, reducing the system's throttling losses is crucial. Throttling losses occur when fluid flow is restricted or regulated by throttling valves, leading to significant pressure drops and energy dissipation. To mitigate these losses, it is essential to minimize the use of throttling systems for regulating flow and pressure. Instead, alternative methods such as variable displacement pumps can be employed to adjust the flow rate and pressure according to the system's demands without causing excessive pressure drops.
Advanced Materials and Sealing TechnoLogies
Material selection plays a critical role in the performance of hydraulic motors. Using advanced sealing materials can significantly reduce friction losses within the motor. Traditional sealing materials often contribute to friction and wear, which not only reduces efficiency but also shortens the lifespan of the motor. Modern sealing materials, designed for low friction and high durability, can help in minimizing these losses.
In addition to seals, the overall material composition of the motor components should be considered. Using lightweight and high-strength materials can reduce the inertia and resistance faced by moving parts, further enhancing the motor's efficiency. Innovations in materials science, such as composite materials and advanced alloys, offer promising solutions to improve the performance and longevity of hydraulic motors.
Maintenance and Contamination Control
Regular maintenance is essential to ensure the efficient operation of hydraulic motors. Over time, Hydraulic Systems can become contaminated with particles, water, and other impurities that increase friction and wear, leading to pressure energy loss. Implementing rigorous maintenance protocols, including regular inspection and replacement of filters, can prevent contamination and ensure the hydraulic fluid remains clean and effective.
Developing new contamination detection methods is also vital. Online measurement of contamination levels allows for real-time monitoring and timely intervention. Advanced sensors and diagnostic tools can detect early signs of contamination, enabling maintenance personnel to address issues before they escalate and cause significant losses.
Collaborative Efforts for Optimal Performance
Reducing pressure energy loss in hydraulic motors is not solely the responsibility of manufacturers; consumers also play a crucial role. Manufacturers should focus on designing and producing motors with optimized internal structures, advanced materials, and reliable sealing technologies. At the same time, consumers must adhere to recommended maintenance schedules and practices to ensure the motors operate efficiently.
Education and training for maintenance personnel are also important. Ensuring that the individuals responsible for the upkeep of hydraulic systems are well-versed in the latest maintenance techniques and technologies can significantly reduce the likelihood of pressure energy losses.
Conclusion
In conclusion, reducing pressure energy loss in hydraulic motors requires a multifaceted approach that includes optimizing internal structures, utilizing advanced materials and sealing technologies, maintaining rigorous contamination control, and fostering collaboration between manufacturers and consumers. By addressing these areas, the efficiency and longevity of hydraulic motors can be greatly enhanced, leading to more sustainable and cost-effective industrial operations. The ongoing advancements in hydraulic technology promise continued improvements in the performance and reliability of these critical components.
Why Choose XingYing Hydraulic as Your Supplier?
1.Direct from Manufacturer: Benefit from competitive pricing on top-quality hydraulic products, sourced directly from our factory in China.
2.Custom Solutions: Our expertise allows us to tailor hydraulic components to your precise requirements, ensuring optimal performance.
3.Reliable Supply: Count on us as your trusted supplier for consistent quality and timely delivery, backed by our reputation in the industry.