How to Avoid Cavitation in Rexroth Hydraulic Pumps
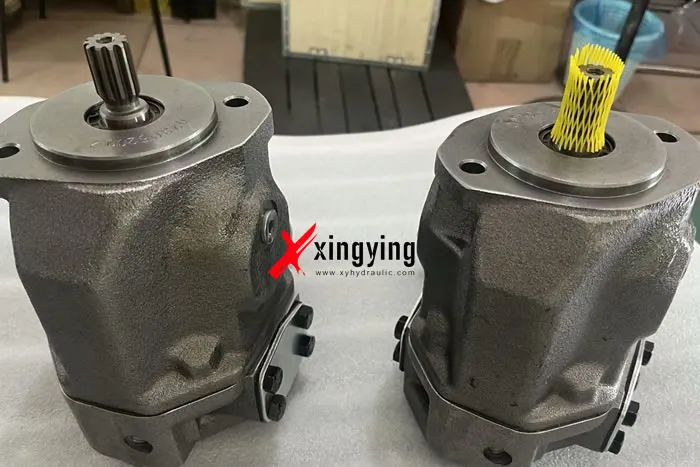
How to Avoid Cavitation in Rexroth hydraulic pumps
When a Rexroth hydraulic pump operates for an extended period, it can develop various issues, with cavitation being one of the most common. Cavitation in hydraulic pumps fundamentally arises due to factors related to the pump itself and the suction installation. Understanding and addressing these factors can help prevent cavitation. This article explores the causes and prevention methods for cavitation in Rexroth Hydraulic Pumps.
What is Cavitation?
Cavitation occurs when the pressure of the liquid drops below its vapor pressure at a given temperature, causing bubbles to form. These bubbles then collapse when they move into higher pressure regions, leading to high-speed liquid impacts and potentially severe damage to the pump components.
Causes of Cavitation
Cavitation typically results from:
- High Geometric Suction Height: Excessive height between the pump and the liquid source can lead to low pressure at the pump inlet.
- High Inhalation Losses: Factors like small pipe diameters, long pipe lengths, and numerous elbows and fittings increase pressure loss in the suction line.
- High Flow Rates: Prolonged operation at high flow rates can cause pressure drops.
- Improper Pump Design: Single-suction pumps are more prone to cavitation compared to double-suction pumps at the same speed and flow rate.
- Inadequate Suction Pool Conditions: Poor conditions at the pump suction pool can significantly impact cavitation.
- Corrosive Operating Conditions: Pumps operating under harsh conditions may suffer from vapor corrosion, accelerating cavitation damage.
Methods to Prevent Cavitation
- Reduce Geometric Suction Height: Lowering the height between the liquid source and the pump can help maintain higher pressure at the pump inlet.
- Minimize Inhalation Losses: Use larger diameter pipes, shorten the length of suction lines, and reduce the number of elbows and fittings.
- Avoid High Flow Rates: Limit the operation time at high flow rates to prevent excessive pressure drops.
- Use Double-Suction Pumps: These pumps reduce the inlet flow rate, making cavitation less likely.
- Adjust Flow and Speed: If cavitation occurs, reduce the flow rate or the pump's operational speed.
- Optimize Suction Pool Conditions: Ensure the suction pool is designed to provide stable and sufficient liquid supply to the pump.
- Use Corrosion-Resistant Materials: In harsh operating conditions, use materials that resist vapor corrosion to extend the pump's lifespan.
Understanding Cavitation Collapse
When bubbles formed during cavitation collapse, the surrounding liquid rushes in to fill the void at very high speeds. This results in intense impacts and high-frequency stresses on the pump components, leading to potential damage such as pitting and erosion.
Effects of Cavitation
Cavitation can lead to:
- Noise and Vibration: The collapsing bubbles cause noise and vibrations, indicating cavitation.
- Reduced Pump Performance: Cavitation can degrade the pump's efficiency and functionality.
- Physical Damage: Continuous cavitation can cause significant wear and tear, leading to the failure of the pump.
Conclusion
Preventing cavitation in Rexroth hydraulic pumps involves careful consideration of both the pump design and the installation conditions. By following the methods outlined above, you can minimize the risk of cavitation, ensuring efficient and long-lasting pump operation.
Understanding and addressing the causes of cavitation not only prolongs the life of the hydraulic pump but also enhances its performance, ultimately saving on maintenance and replacement costs.
Why Choose XingYing Hydraulic as Your Supplier?
1.Direct from Manufacturer: Benefit from competitive pricing on top-quality hydraulic products, sourced directly from our factory in China.
2.Custom Solutions: Our expertise allows us to tailor hydraulic components to your precise requirements, ensuring optimal performance.
3.Reliable Supply: Count on us as your trusted supplier for consistent quality and timely delivery, backed by our reputation in the industry.