Concepts, Mechanical Principles and Installation Considerations of Piston Pumps
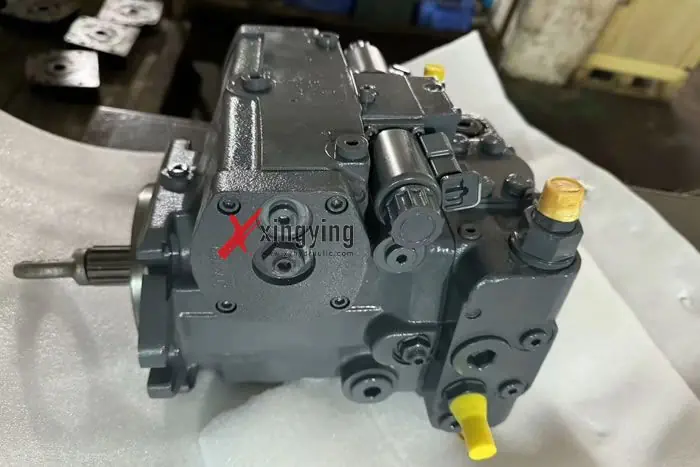
Piston pump is an important device of the Hydraulic System. It relies on the plunger reciprocating movement in the cyLinder, so that the volume of the sealed working chamber changes to realize the suction,pressure oil.
First, the concept of piston pump:
Plunger pump is an important device of the hydraulic system. It relies on the plunger reciprocating movement in the cylinder, so that the volume of the sealed work chamber changes to realize the suction and pressure oil. Plunger pumps have the advantages of high rated pressure, compact structure, high efficiency and easy flow adjustment. Piston Pumps are widely used in high-pressure, large flow and flow need to be adjusted occasions, such as hydraulic presses, engineering machinery and ships.
Second, the mechanical principle of piston pump:
(1) Overview:
Plunger pump plunger reciprocating motion of the total stroke L is constant, determined by the lift of the cam. The size of the oil supply per cycle of the plunger depends on the oil supply stroke, the oil supply stroke is not controlled by the camshaft is variable. The starting moment of oil supply does not change with the change of oil supply stroke. Turning the plunger can change the end moment of oil supply, thus changing the amount of oil supply. When the plunger pump works, the cam on the camshaft of the injection pump and the plunger spring force the plunger to make upward and downward reciprocating motion, so as to complete the pumping task, the pumping process can be divided into the following two stages.
(2) Oil intake process:
When the raised part of the cam turns over, under the action of the spring force, the plunger moves downward, the upper space of the plunger (known as the pumping chamber) generates a vacuum, and when the upper end of the plunger opens the oil inlet hole on the plunger sleeve, the diesel fuel filled in the oil channel of the upper body of the oil pump enters the pumping chamber through the oil hole, and the plunger moves to the lower stopping point, and the oil inletting process ends.
3) Oil return process:
The plunger upward oil supply, when up to the plunger on the slanting groove (stop supply side) and the sleeve on the oil return holes connected, the pump room low-pressure oil and the head of the plunger and radial holes and slanting groove communication, the oil pressure suddenly dropped, the oil valve in the action of the spring force to close quickly, to stop supplying oil. Thereafter, the plunger will have to go up, when the cam cam part of the turn over, under the action of the spring, the plunger and down. At this point the next cycle begins. Plunger pump to a plunger for the principle of introduction, a plunger pump has two check valves, and the direction of the opposite, the plunger to a direction of movement of the cylinder appears negative pressure, then a check valve to open the liquid is sucked into the cylinder, the plunger to another direction of movement, the liquid will be compressed after the other check valve is opened, the liquid is sucked into the cylinder is discharged. This way of working forms a continuous oil supply after continuous movement.
Third, the piston pump installation precautions:
(1) poor self-absorption of hydraulic pumps should be avoided in its suction pipe equipped with a filter
Figure 1a shows, poor self-absorption of the hydraulic pump if the suction port and then installed filters, with the filter pressure drop increases day by day, the minimum suction pressure of the hydraulic pump will not be guaranteed, resulting in insufficient suction of the hydraulic pump, the volumetric efficiency also decreased dramatically, and vibration and noise until the damage to the hydraulic pump. So it should be good as shown in Figure 1b.
Figure 1 hydraulic pump suction circuit program comparison
(2) piping, to avoid causing excessive hydraulic pump suction resistance
As shown in Figure 2a, the hydraulic pump suction line has several sections of hard pipe, shut-off valves, filters and a section of hose, which requires more pipe fittings. Visible total pressure loss on the pipeline will be very large, if the piping and then cause the pipeline local through-flow area becomes smaller, the problem will be more serious, resulting in insufficient hydraulic pump suction, until the hydraulic pump damage. So it should be as shown in Figure 2b. If hoses and shut-off valves are essential, the diameter should be increased to ensure that the suction pressure required by the hydraulic pump.
Figure 2 Comparison of hydraulic pump suction piping options
(3) Avoid connecting the drain pipe of the Relief valve to the suction pipe of the hydraulic pump.
If the relief valve discharge pipe is connected to the suction pipe of the hydraulic pump, because the relief valve discharges hot oil, will make the hydraulic pump and even the entire hydraulic system temperature rise, and is a vicious circle, ultimately leading to component or system failure. Figure 3 shows a comparison of the hydraulic pump's relief oil pipe connection scheme.
(4) to avoid the hydraulic pump's external leakage pipe connected to the pump suction pipe
Because the hydraulic pump's external leakage oil pipe discharges hot oil, it is easy to increase the temperature of the pump body, which is detrimental to the service life of the pump. In addition, in some cases, the pump's external leakage pipe is connected to the pump's suction pipe, but also cause the pump body is not filled with the required hydraulic oil, which is even more unfavorable. Figure 4 shows a comparison of the hydraulic pump's external leakage tubing connection options.
Why Choose XingYing Hydraulic as Your Supplier?
1.Direct from Manufacturer: Benefit from competitive pricing on top-quality hydraulic products, sourced directly from our factory in China.
2.Custom Solutions: Our expertise allows us to tailor hydraulic components to your precise requirements, ensuring optimal performance.
3.Reliable Supply: Count on us as your trusted supplier for consistent quality and timely delivery, backed by our reputation in the industry.